Basic Introduction
Threaded fittings are a commonly used type of pipe fitting, utilized for connecting and sealing pipes through threaded connections. Below is a detailed introduction to threaded fittings:
Application:
Threaded fittings find wide applications across various industries and fields, including petroleum, chemical, natural gas, water treatment, pharmaceuticals, metallurgy, etc. They are commonly used for pipeline connections, conveying fluids, gases, dust, etc.
Materials:
The selection of materials for threaded fittings depends on their application environment and medium characteristics. Common materials for threaded fittings include stainless steel (such as 304, 316), carbon steel, copper, cast iron, etc. Different materials possess different corrosion resistance, pressure resistance, high-temperature performance, and mechanical strength, necessitating selection based on specific application requirements.
Classification:
Threaded fittings can be classified into several types based on different connection methods and structures:
- Internal Threaded Fittings: Threaded fittings with internal threads, generally used for connecting pipes with external threads.
- External Threaded Fittings: Threaded fittings with external threads, generally used for connecting pipes with internal threads.
- High-pressure Threaded Fittings: Threaded fittings designed for high-pressure applications, with higher pressure resistance.
Standards:
The manufacturing and use of threaded fittings need to comply with certain standards to ensure their quality and performance. Common standards include the American Petroleum Institute (API) standards such as API 5CT, API 5L, International Organization for Standardization (ISO) standards such as ISO 9001, European standards (EN), Chinese National standards (GB/T), etc. These standards specify the dimensions, materials, manufacturing processes, quality requirements, etc., for threaded fittings.
International Threaded Fitting Standard System:
There exists a comprehensive international standard system for threaded fittings, primarily including the following main standards:
- ANSI/API Standards: Standards jointly developed by the American Petroleum Institute (API) and the American National Standards Institute (ANSI), including API 5B, API 5CT, etc.
- ISO Standards: Standards developed by the International Organization for Standardization (ISO), including ISO 9001, ISO 11960, etc.
- EN Standards: Standards developed by the European Committee for Standardization (CEN), including EN 10226, EN 10220, etc.
- GB/T Standards: Standards developed by the Standardization Administration of China (SAC), including GB/T 7307, GB/T 28897, etc.
3 Types of Threaded Fittings and Sealing Surface Forms:
1.Internal threaded fittings are a commonly used type of pipe fitting. They feature internal threads used to connect pipes with external threads.
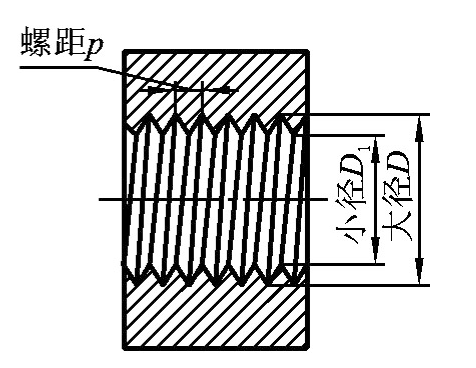
Advantages:
- Convenient Connection: Internal threaded fittings offer a simple and convenient connection method. Pipes can be easily connected and disconnected by rotation, reducing installation time and procedures.
- Secure Fastening: Internal threaded fittings achieve pipe connection and fastening through the tightening and sealing design of threads. They exhibit high sealing performance in high-pressure environments, effectively preventing leaks.
- Strong Durability: Internal threaded fittings are typically manufactured from high-strength materials, offering good pressure resistance, corrosion resistance, and wear resistance, suitable for various working conditions and environments.
- Strong Adaptability: Internal threaded fittings are suitable for various pipe materials and diameters. They can connect pipes of different sizes and adapt to the requirements of different media and working pressures.
Disadvantages:
- Preprocessing Required for Installation: Unlike welded connections, internal threaded fittings require preprocessing for connection, including cutting and machining internal threads at the pipe ends. This increases the complexity and time cost of installation.
- Not Suitable for High-Temperature and High-Pressure Environments: Due to the structure of internal threaded fittings, their ability to withstand high-temperature and high-pressure environments is relatively weak. In high-temperature and high-pressure applications, threaded fittings with higher pressure resistance need to be used.
2.External threaded fittings are a commonly used type of pipe fitting. They feature external threads used to connect pipes with internal threads.
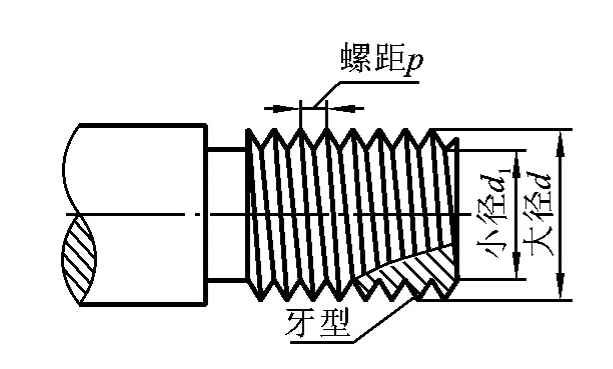
Advantages:
- Convenient Connection: External threaded fittings offer a simple and convenient connection method. Pipes can be easily connected and disconnected by rotation, reducing installation time and procedures.
- Secure Fastening: External threaded fittings achieve pipe connection and fastening through the tightening and sealing design of threads. They exhibit high sealing performance in high-pressure environments, effectively preventing leaks.
- Strong Durability: External threaded fittings are typically manufactured from high-strength materials, offering good pressure resistance, corrosion resistance, and wear resistance, suitable for various working conditions and environments.
- Strong Adaptability: External threaded fittings are suitable for various pipe materials and diameters. They can connect pipes of different sizes and adapt to the requirements of different media and working pressures.
Disadvantages:
- Preprocessing Required for Installation: Unlike welded connections, external threaded fittings require preprocessing for connection, including cutting and machining external threads at the pipe ends. This increases the complexity and time cost of installation.
- Not Suitable for High-Temperature and High-Pressure Environments: Due to the structure of external threaded fittings, their ability to withstand high-temperature and high-pressure environments is relatively weak. In high-temperature and high-pressure applications, threaded fittings with higher pressure resistance need to be used.
3.High-pressure threaded fittings are a special type of threaded fitting designed for high-pressure applications.
Advantages:
- High Pressure Resistance: High-pressure threaded fittings utilize special structural designs and materials, offering high pressure resistance. They can withstand pressure better in high-pressure environments and effectively prevent leaks.
- Strong Corrosion Resistance: High-pressure threaded fittings are typically made from corrosion-resistant materials such as stainless steel, allowing them to be used for extended periods in harsh working environments while maintaining good corrosion resistance.
- Convenient Maintenance and Replacement: High-pressure threaded fittings feature simple structures and convenient installation, making maintenance and replacement easy and reducing maintenance costs and time.
Disadvantages:
- Higher Technical Requirements for Installation: Installation of high-pressure threaded fittings is relatively complex and requires higher technical skills from operators to ensure the tightening and sealing performance of the fittings.
- Limited to Smaller Diameters and Higher Pressure Ranges: Due to the structural and manufacturing limitations of high-pressure threaded fittings, their application range is usually limited to smaller diameters and higher pressure ranges.